The success of TeplEko brand products lies in the constant renewal of the plant’s production facilities.
Ultra – modern equipment, qualified personnel and multi – level system are the guarantee of unquestionable quality of our quartz heaters supplied throughout Russia and former CIS countries.
TeplEko employees constantly follow the innovations on the world thermal equipment market so all models of quartz heaters comply with international standards.
A unique heating element used by TeplEko
Unique
development
A unique heat – resistant chrome – nickel heating element has been developed for TeplEko which has a high resistivity and exceeds 98% efficiency. Zigzag laying of the heater allows to create a uniform heat flow over the entire surface of the monolithic panel. The heating element inside the quartz heater is durable as it does not come into contact with the external environment. Its service life exceeds 25 years.
Heating
element
One of the most important elements of any electric heater is its heating element. It has the highest temperature and basically determines the operability of the heat – emitting structure.
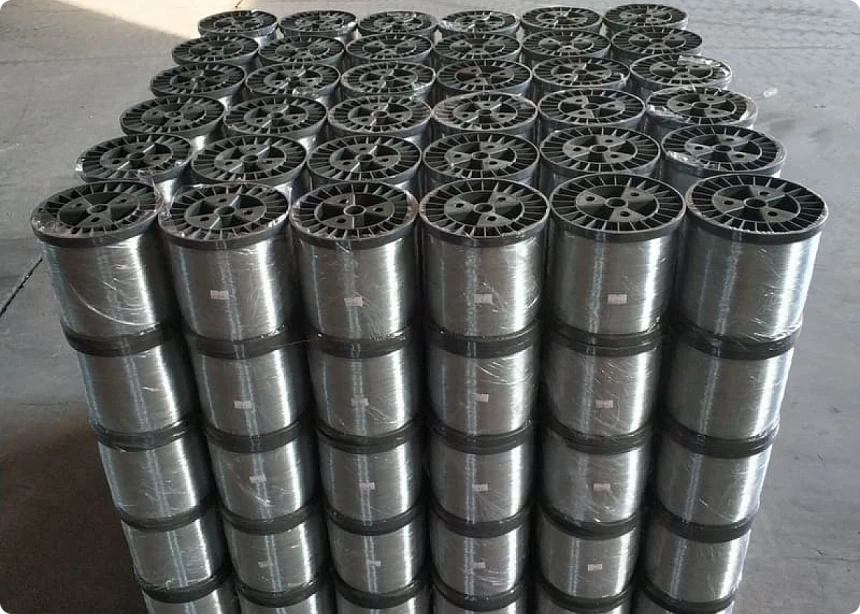
Technological Stages
of Production
Preparation of raw materials
The initial components (quartz sand, refractory environmental binders and additives) for the manufacture of monolithic slabs are stored in a closed warehouse of the company. In order to increase the strength of a monolithic slab, highly refined quartz sand has several fractions as its main component.
At this stage, the composition of the quartz heater components is carefully monitored by the specialists of the factory laboratory. They are pre-processed, sorted and subjected to radiation control.
Preparation of the mass
The initial components are carefully prepared. The technology involves grinding, sieving and weighing the components. Then they are mixed and fed into the RBU installation, manufactured according to a special technical specification. The mass preparation process is automatic, eliminating the appearance of errors in the composition of the final product. The operator monitors the readings on the display and controls the process.
The internal fittings of the heater are filled with the solution. Our own rebar production line is provided by a special sharpening machine. The reinforcement stiffens the structure, protects it from cracks and chips during transportation and operation. Strict adherence to technology and compliance with the proportions of the components makes it possible to eventually obtain a monolithic quartz heater plate with the necessary parameters.
Manufacturing of aluminum frame
The basis (frame) of the energy-efficient quartz heater TeplEco is a frame made of aluminum profile. It is made at the argon welding factory site. The reinforced aluminum profile stiffens the structure and protects it from physical influences.
The reinforcing frame also serves as a mold that is filled with a quartz sand-based mortar mixture, having previously placed a 0.4 kW zigzag heater in it. In the paint chamber, the frame is protected from corrosion by evenly spraying two-component powder paint over its surface.
Molding and drying
At this stage, the TeplEco quartz heater takes on its final shape. To do this, a mortar mixture of quartz sand and binding refractory components prepared in the RBU installation is evenly distributed inside a reinforcing frame laid on a vibrating table. Under the influence of vibration, the solution is rammed and distributed according to the shape of the frame, while covering the heating element.
The structural pattern on the surface of the monolith is created by laying a plastic mold on its surface. Next, the product is placed in a drying chamber, where it is subjected to thermal drying for 4 days. The formed monolith gets rid of moisture, acquires maximum strength and necessary thermophysical parameters.
Calibration and grinding
To reduce porosity and give the surface of the quartz heater an aesthetic appearance, the monolithic panels that have been dried are sanded. The final stage of quartz heater production is quality control. In the quality control area, the company's employees check the operability of the products by connecting them to the network for a long time and measuring the heating of the surfaces.
In the presence of external defects (cracks, chips, etc.), as well as malfunction of the device or manufacturing technology, quartz heaters are rejected. Defective samples account for only a fraction of a percent of the total volume of finished products. All the controlled devices are packed and moved to the warehouse.
Packing
For safe transportation, the TeplEco heater is supplied in a branded cardboard package. Packaging of products is carried out on machines, which reduces the cost and final price of the goods. The informative box clearly demonstrates the quality of our products and TeplEco's market prospects.
The labels carry useful information about technical specifications, precautions, and operating recommendations. A protective film is used to protect the device and the packaging itself from mechanical and climatic influences.
Laser cutting
The competitive advantage of TD TeplEco is the availability of its own full production cycle of compact quartz heaters, as well as some accessories for them, such as brackets, stands, etc. The components are manufactured in the laser cutting workshop using compressed oxygen and solid metal sheets. Laser machines allow metalworking to be carried out with exceptional precision using pre-designed diagrams and drawings.
When used in combination with other metalworking methods (bending, welding, powder coating), this process is ideal. The products produced by TeplEco are distinguished by their impeccable accuracy of linear dimensions and angles.
Gallery
In the above photos, you can get acquainted with the stages of the full production cycle of innovative quartz heaters fr om TeplEco. In the photo gallery, we have tried to display the sequence of production operations, thanks to which the raw materials are transformed into finished products.
TeplEco has warehouses for raw materials, huge environmentally friendly production areas, many workshops (assembly, molding, painting, drying, argon welding, laser cutting, etc.), as well as a warehouse for finished products, from wh ere we ship quartz heaters to dozens of branded stores throughout the country and abroad.
We will answer your
questions
Leave a request. We will get in touch with you shortly.